玻璃纤维复合材料(GFRP)凭借其轻量化、高强度和耐腐蚀等特性,已成为航空航天、汽车制造、建筑及电子等领域的核心材料。传统机械切割易导致纤维断裂、边缘分层等问题,而新型切割技术的引入显著提升了加工精度与效率。本文系统梳理当前主流切割技术,分析其原理、适用场景及技术瓶颈,为相关行业中的企业提供技术选型参考。
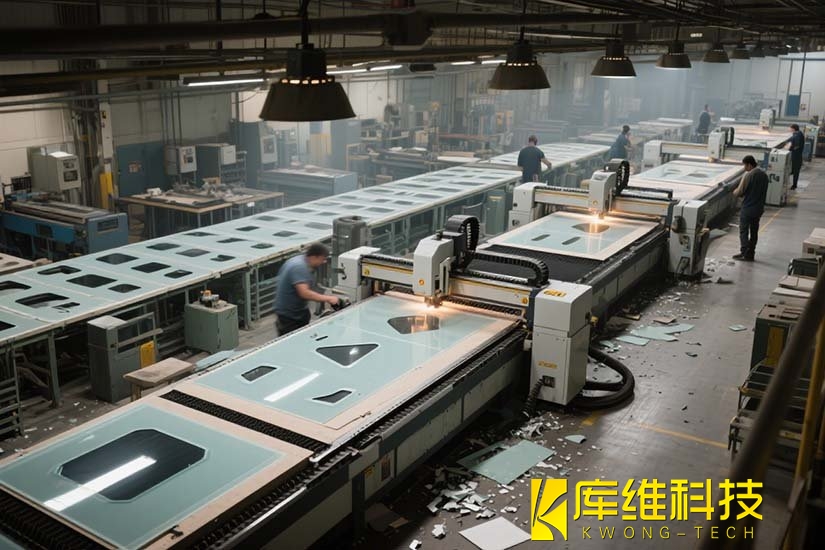
一、激光切割技术
1、技术原理
激光切割通过高能激光束聚焦于材料表面,使局部区域瞬间汽化或熔融,形成切口。针对玻璃纤维复合材料,光纤激光(波长1070nm)因穿透力强、光束质量优,成为主流选择;而CO₂激光(波长10.6μm)因对树脂基体吸收率更高,适用于特定场景。
2、工艺优化
参数控制:激光功率(800-2000W)、扫描速度(200-500mm/s)及离焦量需协同调整。研究表明,功率1000W、速度300mm/s时,切口粗糙度Ra≤6.3μm,热影响区(HAZ)宽度<50μm。
辅助气体:采用氮气(N₂)或压缩空气可减少氧化和毛刺,提升切割面光洁度。
3、应用场景
航空航天:飞机内饰板、舱门框架的复杂轮廓切割。
电子制造:PCB基板开槽及微小孔加工(孔径≥0.2mm)。
局限性:高反射率区域(如碳纤维区域)需预处理,且设备成本较高。
二、水导激光切割
1、技术突破
水导激光将激光束通过高压水柱(300-600MPa)传导,利用水的冷却效应抑制热扩散,同时水射流辅助排屑。该技术将热影响区降低至<10μm,纤维断裂率减少70%。
2、性能对比
3、典型应用
汽车工业:电池包壳体、碳纤维增强部件的精密加工。
医疗器械:骨科植入物(如骨板)的微结构切割。
三、机械切割技术
1、锯切与钻孔
金刚石锯片:适用于厚板(>10mm)直线切割,转速控制在1500-3000rpm,进给率0.5-2m/min,可减少分层。
PCD钻头:针对碳纤维/玻璃纤维叠层材料,采用“啄钻”工艺(每钻入3mm退刀排屑),孔出口端分层率降低至<15%。
2、铣削与磨削
硬质合金铣刀:加工角度需与纤维方向成±45°,避免层间剥离。
碳化硅砂轮:湿磨条件下,粒度80-120目可平衡效率与表面质量(Ra≤3.2μm)。
四、新兴技术
1、振动刀切割
通过高频微幅振动(>20kHz)实现无接触切割,适用于超薄材料(<1mm),切口边缘无热损伤,但设备投资较高(约¥50-80万/台)。
2、混合加工系统
集成激光与水刀的复合设备可实现“粗切-精修”一体化流程,效率提升40%,适用于异形件批量生产。
五、技术选型决策矩阵
激光与水导激光技术凭借其热影响小、精度高的优势,已成为高端领域的首选;而机械切割凭借成本低、适用性广的特点,仍在常规加工中占据重要地位。随着复合材料在新能源、氢能储罐等新兴领域的应用扩展,切割技术需进一步突破多材料复合、超厚板加工等技术瓶颈,以满足产业升级需求。